Toyota develops new paint line with reduced environmental burden
The Japanese carmaker has reduced the size of paint line equipment by 40% and decreased CO2 emissions from the line by 32% while maintaining high quality levels.
Toyota has announced that its new paint line, at the Prius production line at the Tsutsumi Plant in Japan, has received the Okochi Memorial Production Prize for a significant reduction in the size of the paint line, and its corresponding CO2 emissions in the 63rd (2016) Okochi Memorial Prize awards.
Presented by the Okochi Memorial Foundation, the Okochi Memorial Prize acknowledges remarkable achievements related to research and development, and the application of production engineering, production technology and production systems annually.
As is known, CO2 is not only emitted by vehicles while traveling, but also during the vehicle manufacturing process. Toyota says it has been striving to reduce CO2 and other Substances of Concern (SoC) that are discharged during the manufacturing of automobiles at production sites. In particular, paint processes discharge the largest quantity of CO2 compared to various other processes in the automobile manufacturing process such as stamping, welding and assembly.
Now, the Japanese carmaker has developed and introduced new paint technology and completely improved all paint processes. As a result, it has successfully reduced the size of paint line equipment by 40% and decreased CO2 emissions from the line by 32% while maintaining high quality levels.
A key point of this technology is the development of production technology that has realized a ‘reduction of process length’, ‘reduction of equipment height’, and ‘reduction of size of associated equipment’.
More specifically, a wide variety of efforts were made such as reducing the space under the paint booth (space to collect leftover paint), creating a narrower booth air supply room, jidoka (automation with a human touch) of the cleaning and interior painting processes*3, improving robot processing capabilities, optimising transfer pitch, decreasing cross-section surface of the dry oven, and effectively using compact deodorisation equipment.
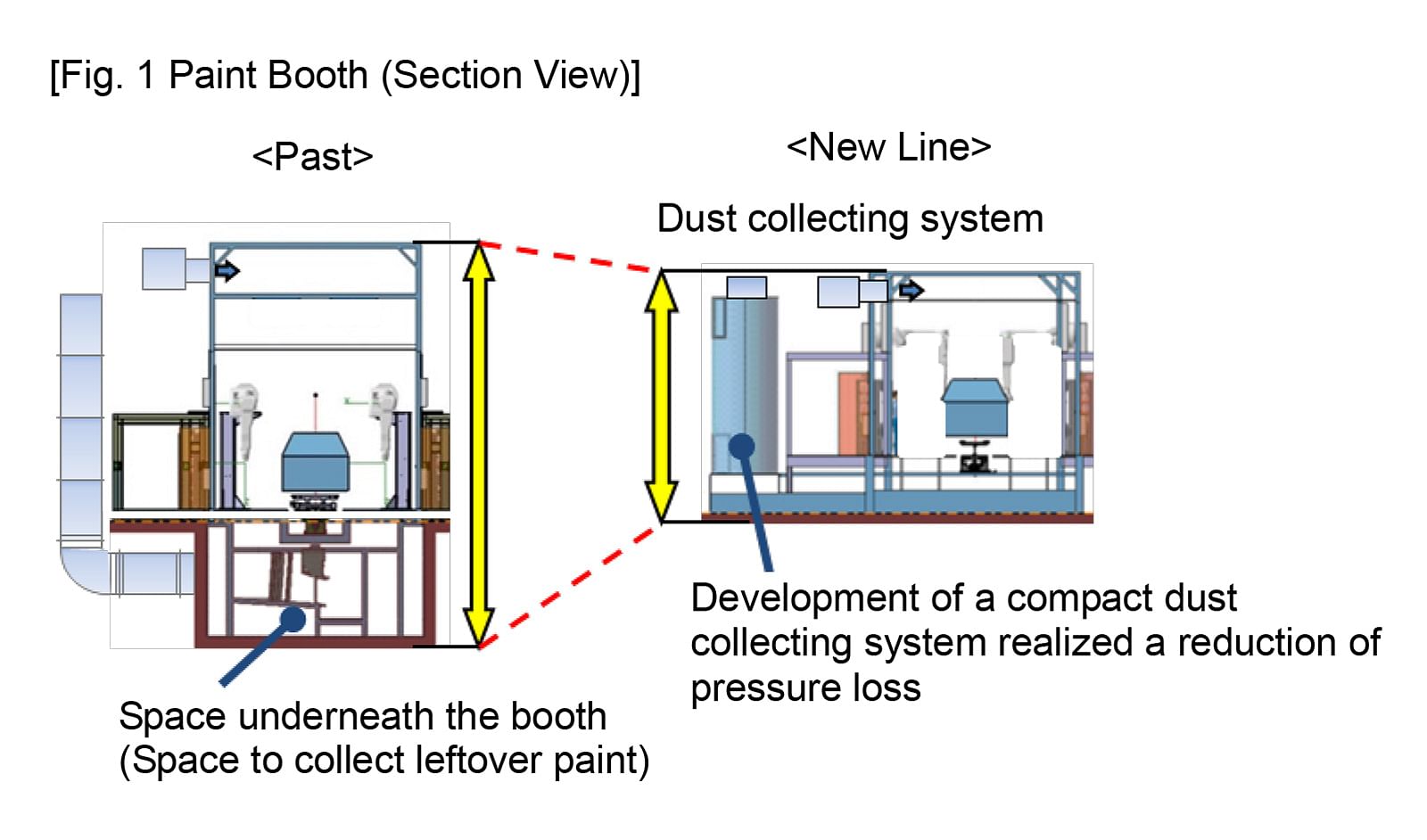
Reducing the space beneath the paint booth had the greatest contribution to the reduction of line size. Toyota's development of a new method using centrifugal force to collect paint that did not adhere to car bodies, reduction of equipment size, and decrease of pressure loss also contributed to CO2 emission cuts.
Currently, the paint line that adopted this technology is used for the production of the Prius, which is one of the most popular environmentally friendly Toyota models. Its deployment to other plants in Japan and overseas has also been scheduled.
RELATED ARTICLES
Hyundai unveils next−gen highly efficient hybrid system
The next-gen hybrid system is claimed to offer 45% better fuel efficiency and 19% more power compared with ICE powertrai...
Horse Powertrain reveals hybrid conversion for electric cars
Engine-making joint venture of Geely and the Renault Group announces new hybrid powertrain that fits into the same space...
Aisin to produce hybrid motor for Mitsubishi in Thailand
The hybrid drive motor and gearbox, will be produced at Aisin Powertrain (Thailand) Co for use in the Mitsubishi XForce ...