GKN Driveline begins testing ‘All Twinster’ plug-in hybrid SUV
Plug-in hybrid has ‘sailing’ capability to lower CO2 emissions and also features a pure EV mode
GKN Driveline has begun testing a revolutionary SUV technology research vehicle, which showcases its leadership in electrified drivetrains, All-Wheel Drive (AWD) and systems integration. Based on a Mercedes-AMG GLA 45, the one-off GKN Technology Demonstrator 2018 vehicle (GTD18), features mechanical and electric Twinster torque vectoring, a plug-in hybrid system and completely re-engineered control systems.
GKN’s substantial re-engineering of the standard road car means that the petrol-powered SUV with hang-on AWD ‘torque on demand’ functionality has become a petrol-electric plug-in hybrid with a zero-emissions pure-electric drive mode, and axle-split eAWD functionality that is independent of the combustion engine. Torque vectoring by GKN’s award-winning Twinster system is available on all four wheels, which is a world first.
Following initial testing at GKN Driveline’s Lohmar R&D centre in Germany, the GTD18 begins more extensive validation and proof-of-concept demonstrations this month at the company’s Wintertest facility in northern Sweden. This year marks the 30th anniversary since GKN first started testing and demonstrating technologies at its dedicated vehicle development facility just outside the Arctic Circle.
Unique 'All Twinster' driveline
For the front axle drive, GKN’s technical showcase harnesses the donor car’s 280 kW (381 PS) four-cylinder powertrain, and integrates a mechanical Twinster unit directly to the gearbox, replacing the final drive and differential. This allows GKN’s software to have complete control of torque distribution through the unique twin-clutch system that can make rapid and precise adjustments between the front left and right wheels by application of torque vectoring.
As part of the complete tear-down of the brand-new donor vehicle, the front Power Transfer Unit, propshaft and rear axle were all removed. In their place, at the rear of the car, GKN has integrated its new two-speed eAxle – ‘eTwinsterX’ and a high-performance battery. Despite a high output of 120 kW (163 PS) and 210 Nm (155 lb ft) of torque, the integrated e-motor’s coaxial format means that the electric drive (eDrive) unit is significantly smaller than other systems with equivalent power outputs. This allows it to easily integrate within existing vehicle platforms, providing ‘bolt on’ eAWD hybridisation. The eTwinsterX system also features a GKN-designed two-speed transmission, as well as full torque vectoring capability.

The unique ‘All Twinster Hybrid System’ setup of the demonstrator car means that GKN can precisely control the distribution of torque to all four wheels. New electronic control units (ECUs) were installed to govern the dynamics of the one-of-a-kind driveline, and all software was developed and calibrated by GKN engineers. This also extended to the integration of GKN’s hardware and software with the standard car’s systems, to ensure that the electric drive at the rear runs in harmony with the petrol powertrain at the front.
New dynamics and efficiency
GKN’s eTwinsterX system gives the GTD18 an extraordinary level of agility, with unprecedented all-wheel torque vectoring capabilities, including the capability to over-speed the outside wheel in a corner to induce a yaw moment, helping to bring the car into a tighter line when turning.
The transformation of the GLA45 from an all-wheel-drive internal combustion engine-powered car to a technology demonstrator, incorporating a number of distinct drive modes, showcases GKN’s extensive capabilities in complex and sophisticated vehicle integration.
The driving modes – which are switchable ‘on-the-fly’ – can be selected via a touch pad inside the car. The eTwinsterX system allows for a pure-electric, zero-emissions drive mode through the rear wheels. Conversely it can also operate in solely front-wheel drive mode. The combination of the two delivers a hybrid eAWD mode with the two powertrains working together.
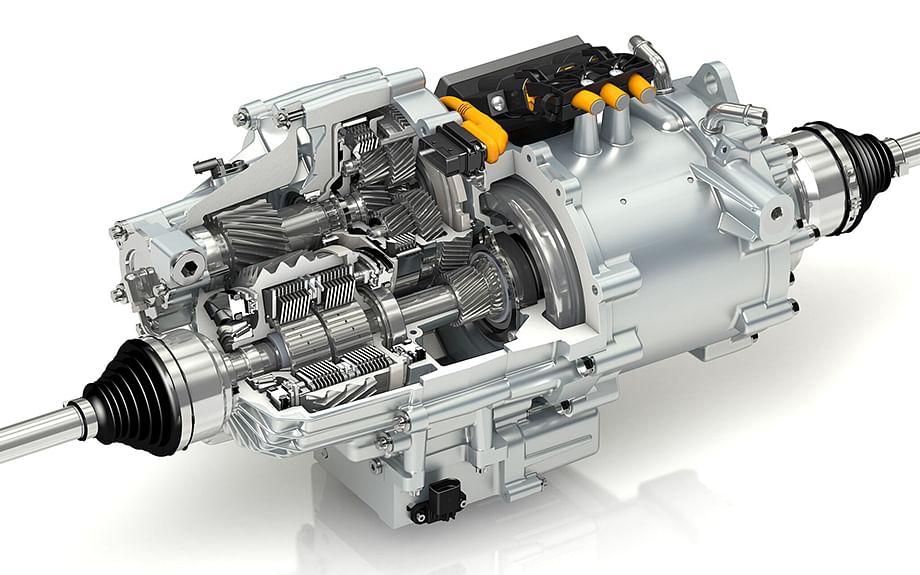
Re-engineered with 1,340 new parts
The build involved significant re-engineering work. As well as relocating several components, new hardware was introduced, including a new bespoke rear subframe to integrate the eTwinsterX system, a new high-capacity battery under the rear seats, a new exhaust system, and new wiring looms. In addition, new ECUs were integrated with the existing Mercedes-AMG software control systems. In total, 99 assemblies needed significant mechanical or electrical modifications, resulting in 1,340 new parts being added to the vehicle.
Almost every piece of the new technology in the car is a functional sample or an early-stage prototype, so GKN says it created several hardware-in-loop (HIL) sub-systems in parallel, to identify and solve any installation and integration issues in the car.
Also read: Dana to merge with GKN's Driveline Division
RELATED ARTICLES
Hyundai unveils next−gen highly efficient hybrid system
The next-gen hybrid system is claimed to offer 45% better fuel efficiency and 19% more power compared with ICE powertrai...
Horse Powertrain reveals hybrid conversion for electric cars
Engine-making joint venture of Geely and the Renault Group announces new hybrid powertrain that fits into the same space...
Aisin to produce hybrid motor for Mitsubishi in Thailand
The hybrid drive motor and gearbox, will be produced at Aisin Powertrain (Thailand) Co for use in the Mitsubishi XForce ...