Why Ford secretly plants faulty parts onto its assembly line in Valencia
Ford's 'Gremlin Tests' help realise the quality, alongside industry-first digital photo tech that records, checks and traces all vehicle parts at mega-plant in Valencia, Spain.
Ford employees are tasked with secretly planting wrong and faulty parts onto the assembly line, including incomplete steering wheels and faulty engine components, as part of a process to ensure all new vehicles built at the plant in Valencia meet Ford’s rigorous quality standards.
Xabier Garciandia’s working day involves literally trying to put a spanner into the works of one of the world’s most advanced auto plants – by making sure wrong parts and faulty components are secretly placed on the assembly line.
Ford’s industry-first Vision System photographs, checks and tracks every single part of each of the 400,000 cars and vans assembled, and 330,000 engines built at the Ford Valencia plant each year.
“Gremlin Tests are an innovative way of ensuring that each process is working correctly,” said Ford in an official statement.
Explaining the unusual testing methods, Garciandia, technical specialist, Valencia Engine Vision System, Ford of Europe said, “The Vision System is crucial to ensuring every single part of each vehicle is just right. The ‘Gremlin Test’ means we can ensure the system is working perfectly. It is a game with a very serious point; we are making them harder to spot all the time.”
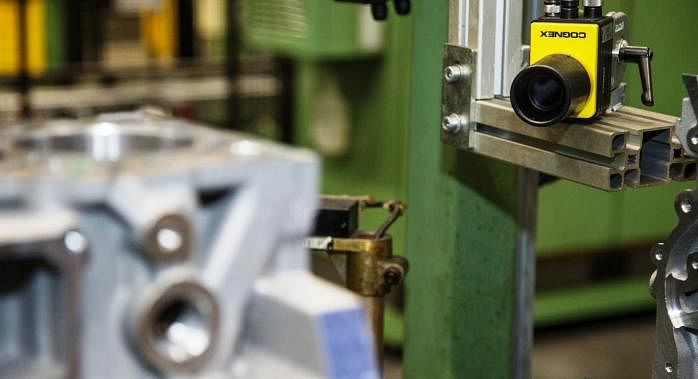
Vision System photographs check and track every single part
Ford produces more Ford models at the state-of-the-art Ford mega-plant in Valencia than anywhere else in Europe, including Kuga, Kuga Vignale, Mondeo, Mondeo Vignale, Galaxy, S-MAX and Transit Connect and Tourneo Connect. Ford’s 2.0-litre and 2.3-litre Ecoboost engines are also built at the plant.
The Vision System captures more than a billion photos every 14 days, comparable to the number of photos uploaded to Instagram in Europe. * This also helps to generate a composite image – consisting of 3,150 digital photographs – that highlights any discrepancies to engineers on the spot.
Faulty engine parts, wrong steering wheels, and even incorrect dashboards have been sent down the line, with the ‘Gremlin Test’ now extended to all 34 stages of assembly.
“The way in which we all use digital cameras has totally changed the way we record our daily way of life, and is now transforming the way we build engines and cars. But we also have to test the tests, and we are doing this in a way that is very simple, but which we believe is unique in the auto industry,” said Garciandia.
Ford has introduced a range of rigorous and in some instances unusual quality processes at the plant where a new vehicle rolls off the production line every 40 seconds.
More from Ford:
- New Smartphone app enables workers to make on-the-spot quality checks
RELATED ARTICLES
Horse Powertrain reveals hybrid conversion for electric cars
Engine-making joint venture of Geely and the Renault Group announces new hybrid powertrain that fits into the same space...
Aisin to produce hybrid motor for Mitsubishi in Thailand
The hybrid drive motor and gearbox, will be produced at Aisin Powertrain (Thailand) Co for use in the Mitsubishi XForce ...
GM reports strong Q1 sales in China, demand for EVs and hybrids surges 53%
General Motors and its joint ventures in China have sold more than 442,000 units between January and March 2025.