Federal-Mogul expands valve guide, seat and turbo bushing materials to enable greener heavy-duty diesel engines
Federal-Mogul Holdings Corporation’s Powertrain Division has expanded its range of high :performance materials
Federal-Mogul Holdings Corporation’s Powertrain Division has expanded its range of high performance materials for valve guides, seats and turbocharger bushings that support the commercial vehicle industry’s drive towards greener, more efficient engines.
Providing superior wear resistance at elevated temperatures, the new materials use Federal-Mogul’s well-proven powder metal (PM) technology to add other benefits, such as greater corrosion resistance and mechanical strength, depending upon the application.
“Increasing restrictions on exhaust emissions have led to downsized, heavily turbocharged engines with high levels of aftertreatment such as particulate filter systems and selective catalytic reduction (SCR), that run hotter than their predecessors,” explained Frank Zwein, Federal-Mogul’s global application engineering director, Valve Seats and Guides. “This has pushed peak cylinder pressures up from around 180 bar to 230 bar and beyond, while temperatures at the valves and turbocharger can exceed 750°C. The geometric issues can be as challenging as the tribology, because of increased distortion around the cylinder head in combination with valve brake systems introducing side loads onto the valve stems, or higher turbo temperatures affecting press fits through differential expansion.”
To overcome these challenges, Federal-Mogul has added the FM-G15 family to its range of advanced valve guide materials, and two new turbocharger bushing materials, FM-T90A and FM-T82A. “The FM-G15 family has been designed and tailored to meet the specific requirements of heavy-duty, highly complex engine designs in the marketplace today, and those in development for tomorrow,” said Denis Christopherson, Federal-Mogul’s global R&D director, Valve Seats and Guides.
FM-G15 family of advanced valve guide materials
FM-G15A is an alloy developed for high temperature wear resistance and reduced valve stem scuffing through a combination of solid lubricants within a high carbon steel matrix. The solid lubricant package, combined with vacuum oil impregnation, delays valve stem scuffing in high temperature, heavily side-loaded applications.
FM-G15E enhances the performance of FM-G15A by combining wear resistance with superior friction reduction by using a high volume of solid lubricant captured within a heat treated Molybdenum steel microstructure. Vacuum oil impregnation provides additional tribological support and an exceptional combination of machinability and durability. This combination of alloy and manufacturing processes offers significantly better performance than typical valve guide materials.
FM-G15N offers superior durability and wear resistance in applications subjected to excessively high temperatures and side loading. The chromium steel alloy matrix contains a fine distribution of solid lubricants and vacuum oil impregnation for additional performance enhancement beyond that of cast iron or typical powder metal alloys.
Federal-Mogul Valve Seat Insert (VSI) Solutions for Highly Loaded Applications
Federal-Mogul’s VSI portfolio provides materials that use state-of-the-art PM technology to meet the needs of Euro-6 and other advanced engine applications. A family of high alloy PM tool steel-based materials has already proven successful in a wide range of today’s engine designs.
For the demanding requirements of tomorrow’s engines, Federal-Mogul has developed advanced PM alloying and processing techniques, to provide additional performance. These include the addition of wear resistant carbide alloy hard particles, full-density enhanced sintering, and the development of complex phase microstructures.
Latest developments also include the use of hybrid PM tool steel and stainless steel powders, along with performance enhancing additives, to provide the highest corrosion resistance against sulfur and alternative fuels while maintaining the required compressive strength and wear resistance.
Turbocharger Bushing Materials: FM-T90A and FM-T82A
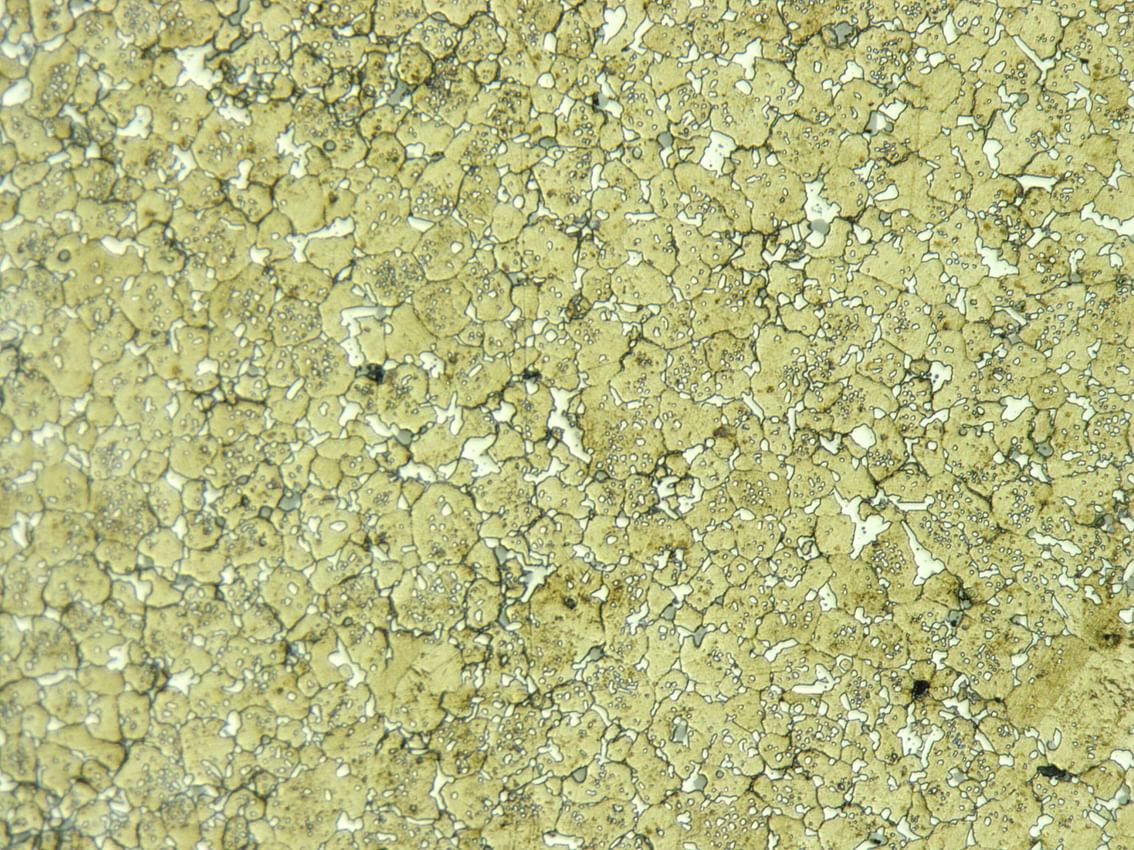
Federal-Mogul’s new advanced turbocharger bushing materials provide exceptional wear performance at elevated temperatures and in highly corrosive environments. FM-T90A (pictured above) is a cobalt-based, fully dense sintered alloy specifically designed for extreme applications up to 1050deg C in corrosive or oxidizing conditions. FM-T90A is superior to ferrous alloys in harsh conditions because it offers the advantages of powder metal technology, such as complex composite microstructures, not attainable by melt and cast techniques. The cobalt matrix with carbide precipitates and solid lubricant particles produces a unique combination of wear and corrosion resistance, along with high strength at elevated temperatures.
FM-T82A is a ferrous-based, fully dense composite material with reduced nickel content to provide a cost-effective solution with exceptional high temperature properties in aggressive turbocharger bushing applications. Comprising a complex microstructure of austenite, alloy carbides and friction-reducing solid lubricant particles, FM-T82A is recommended for operating temperatures high as 1050°C. A derivative of Federal-Mogul’s well-proven 8100 material, it offers improved high temperature strength compared to ferritic alloys, yet maintains oxidation resistance and thermal expansion to match common turbocharger housing materials.
“Customers in the heavy-duty sector are finding that traditional cast materials are no longer adequate for the increasingly aggressive conditions encountered in the latest high-efficiency engines,” said Olaf Weidlich, director and general manager, Valve Seats and Guides. “Our extensive experience with powder metal technology has enabled us to prepare for this with proven solutions. By working with Federal-Mogul, engine manufacturers can meet future challenges with a variety of solutions designed to suit their particular application.”
Federal-Mogul Holdings Corporation’s Powertrain Division has expanded its range of high performance materials for valve guides, seats and turbocharger bushings that support the commercial vehicle industry’s drive towards greener, more efficient engines.
Providing superior wear resistance at elevated temperatures, the new materials use Federal-Mogul’s well-proven powder metal (PM) technology to add other benefits, such as greater corrosion resistance and mechanical strength, depending upon the application.
“Increasing restrictions on exhaust emissions have led to downsized, heavily turbocharged engines with high levels of aftertreatment such as particulate filter systems and selective catalytic reduction (SCR), that run hotter than their predecessors,” explained Frank Zwein, Federal-Mogul’s global application engineering director, Valve Seats and Guides. “This has pushed peak cylinder pressures up from around 180 bar to 230 bar and beyond, while temperatures at the valves and turbocharger can exceed 750°C. The geometric issues can be as challenging as the tribology, because of increased distortion around the cylinder head in combination with valve brake systems introducing side loads onto the valve stems, or higher turbo temperatures affecting press fits through differential expansion.”
To overcome these challenges, Federal-Mogul has added the FM-G15 family to its range of advanced valve guide materials, and two new turbocharger bushing materials, FM-T90A and FM-T82A. “The FM-G15 family has been designed and tailored to meet the specific requirements of heavy-duty, highly complex engine designs in the marketplace today, and those in development for tomorrow,” said Denis Christopherson, Federal-Mogul’s global R&D director, Valve Seats and Guides.
FM-G15 family of advanced valve guide materials
FM-G15A is an alloy developed for high temperature wear resistance and reduced valve stem scuffing through a combination of solid lubricants within a high carbon steel matrix. The solid lubricant package, combined with vacuum oil impregnation, delays valve stem scuffing in high temperature, heavily side-loaded applications.
FM-G15E enhances the performance of FM-G15A by combining wear resistance with superior friction reduction by using a high volume of solid lubricant captured within a heat treated Molybdenum steel microstructure. Vacuum oil impregnation provides additional tribological support and an exceptional combination of machinability and durability. This combination of alloy and manufacturing processes offers significantly better performance than typical valve guide materials.
FM-G15N offers superior durability and wear resistance in applications subjected to excessively high temperatures and side loading. The chromium steel alloy matrix contains a fine distribution of solid lubricants and vacuum oil impregnation for additional performance enhancement beyond that of cast iron or typical powder metal alloys.
Federal-Mogul Valve Seat Insert (VSI) Solutions for Highly Loaded Applications
Federal-Mogul’s VSI portfolio provides materials that use state-of-the-art PM technology to meet the needs of Euro-6 and other advanced engine applications. A family of high alloy PM tool steel-based materials has already proven successful in a wide range of today’s engine designs.
For the demanding requirements of tomorrow’s engines, Federal-Mogul has developed advanced PM alloying and processing techniques, to provide additional performance. These include the addition of wear resistant carbide alloy hard particles, full-density enhanced sintering, and the development of complex phase microstructures.
Latest developments also include the use of hybrid PM tool steel and stainless steel powders, along with performance enhancing additives, to provide the highest corrosion resistance against sulfur and alternative fuels while maintaining the required compressive strength and wear resistance.
Turbocharger Bushing Materials: FM-T90A and FM-T82A
Federal-Mogul’s new advanced turbocharger bushing materials provide exceptional wear performance at elevated temperatures and in highly corrosive environments. FM-T90A is a cobalt-based, fully dense sintered alloy specifically designed for extreme applications up to 1050deg C in corrosive or oxidizing conditions. FM-T90A is superior to ferrous alloys in harsh conditions because it offers the advantages of powder metal technology, such as complex composite microstructures, not attainable by melt and cast techniques. The cobalt matrix with carbide precipitates and solid lubricant particles produces a unique combination of wear and corrosion resistance, along with high strength at elevated temperatures.
FM-T82A is a ferrous-based, fully dense composite material with reduced nickel content to provide a cost-effective solution with exceptional high temperature properties in aggressive turbocharger bushing applications. Comprising a complex microstructure of austenite, alloy carbides and friction-reducing solid lubricant particles, FM-T82A is recommended for operating temperatures high as 1050°C. A derivative of Federal-Mogul’s well-proven 8100 material, it offers improved high temperature strength compared to ferritic alloys, yet maintains oxidation resistance and thermal expansion to match common turbocharger housing materials.
“Customers in the heavy-duty sector are finding that traditional cast materials are no longer adequate for the increasingly aggressive conditions encountered in the latest high-efficiency engines,” said Olaf Weidlich, director and general manager, Valve Seats and Guides. “Our extensive experience with powder metal technology has enabled us to prepare for this with proven solutions. By working with Federal-Mogul, engine manufacturers can meet future challenges with a variety of solutions designed to suit their particular application.”
RELATED ARTICLES
Isuzu unveils D-Max EV at 2025 Commercial Vehicle Show
Revealed at the 2025 Commercial Vehicle Show in Birmingham, the Isuzu -Max EV is the first fully electric commercial pic...
Hyundai unveils next−gen highly efficient hybrid system
The next-gen hybrid system is claimed to offer 45% better fuel efficiency and 19% more power compared with ICE powertrai...
Horse Powertrain reveals hybrid conversion for electric cars
Engine-making joint venture of Geely and the Renault Group announces new hybrid powertrain that fits into the same space...