Alcoa unveils aluminium alloy that’s 40% more formable and 30% stronger
Lightweight metals company Alcoa has unveiled breakthrough manufacturing technology
Lightweight metals company Alcoa has unveiled breakthrough manufacturing technology, the Alcoa Micromill, that will manufacture the most advanced aluminium sheet on the market. The Micromill will enable the next generation of automotive aluminium products, and equip Alcoa to capture growing demand.
The Alcoa-patented Micromill process dramatically changes the microstructure of the metal, allowing the production of an aluminium alloy for automotive applications that has 40 percent greater formability and 30 percent greater strength than the incumbent aluminium used today while meeting stringent automotive surface quality requirements.
Additionally, automotive parts made with Micromill material will be twice as formable and at least 30 percent lighter than parts made from high strength steel. The Micromill alloy has formability characteristics comparable to mild steels.
“Alcoa Micromill represents a major breakthrough in aluminium materials,” said Alcoa chairman and CEO Klaus Kleinfeld. “This technology will unlock the next generation of automotive products with strength, formability and surface quality combinations never before possible. It will allow our customers to redefine the boundaries of vehicle design, supporting the creation of lighter, more fuel efficient, safer and more stylish vehicles for the future.”
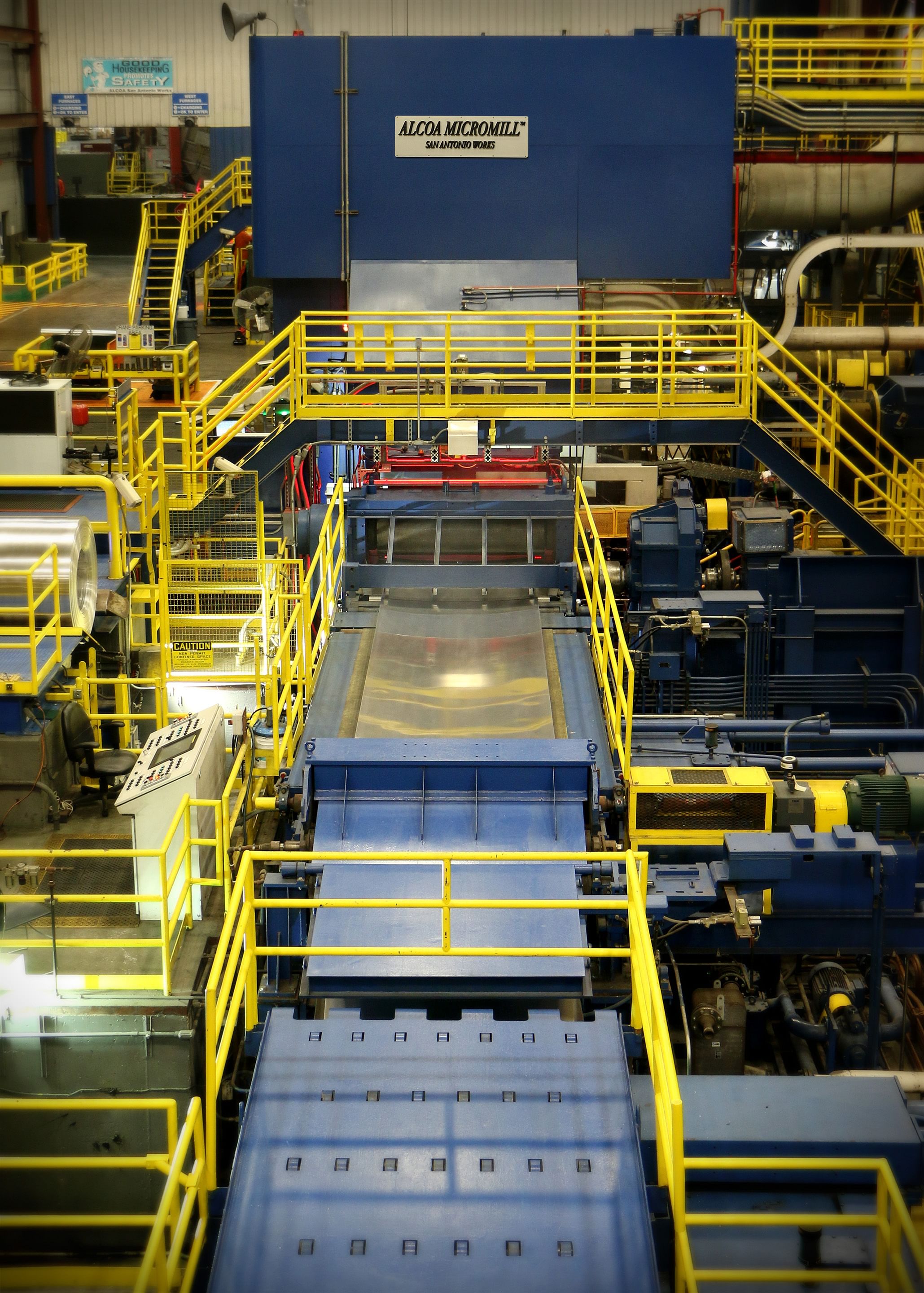
Ideal for auto
Micromill aluminium sheet that is 40 percent more formable is easier to shape into intricate forms, such as the inside panels of automobile doors and external fenders, which today are generally made of steel. The 30 percent increase in material strength will improve dent resistance, enabling the production of automotive sheet that is thinner and even lighter than previous generations. Automakers will also benefit from reduced system cost by streamlining the number of aluminium alloys used in their manufacturing process.
The company says it will also be the fastest, most productive aluminium casting and rolling system in the world. A traditional rolling mill takes around 20 days to turn molten metal into coil, Micromill does it in just 20 minutes.
The Micromill also has a significantly smaller footprint than a traditional rolling mill, at just one quarter the size, and lowers energy use by 50 percent. The Alcoa Micromill technology and the differentiated metal it will produce are covered by more than 130 patents around the world.
According to Ducker Worldwide, North American aluminium automotive sheet content per vehicle is expected to increase 11-fold between 2012 and 2025 as consumers demand cars that are lighter and more fuel efficient. The Micromill continuous casting technology is designed to meet that growing demand for automotive sheet, with the flexibility to serve the industrial and packaging markets as well. The mill can easily shift product mix, and transition to different alloys without ever stopping a cast.
Alcoa has secured a strategic development customer, and from its pilot Micromill facility in San Antonio, TX, has also conducted successful customer trials. Those trials have validated the Micromill material’s unique characteristics, surface quality for exterior panels and overall performance. Alcoa is qualifying the material for use in next-generation automotive platforms.
RELATED ARTICLES
Aisin to produce hybrid motor for Mitsubishi in Thailand
The hybrid drive motor and gearbox, will be produced at Aisin Powertrain (Thailand) Co for use in the Mitsubishi XForce ...
GM reports strong Q1 sales in China, demand for EVs and hybrids surges 53%
General Motors and its joint ventures in China have sold more than 442,000 units between January and March 2025.
Volkswagen to invest $580 million in Argentina, plots new pick-up truck for South America
Volkswagen is paving the way for the next generation of mid-size pick-up truck as a successor to the Amarok. The new mod...